Auswahl des richtigen Schleifmittels für das Schleifen von Leder
Leder ist ein Naturprodukt, das durch Gerbprozesse von Tierhäuten gewonnen wird. Die Naturfaserstruktur bleibt erhalten. Während der Verarbeitung wird zwischen der Narbenseite und der Fleischseite unterschieden.
Wenn Leder geschliffen wird, wird entweder die Lederoberseite (Narbenseite oder Narbenspalt), oder die Rückseite (Fleischseite oder Fleischspalt) mit Schleifpapier bearbeitet. Hierzu wird meist eine mit Schleifpapier bespannte Walze genutzt, die sich auf dem Werkstück dreht und die Lederteile schleift oder poliert. Ziel dieser Verarbeitung ist es, ein einheitliches Erscheinungsbild des Materials zu erreichen.
Wenn die Narbenseite grob geschliffen wird, erhält sie einen leichten Wildstrich. Bei dieser Verarbeitung wird das Leder als Nubukleder bezeichnet.
Um glattes Leder herzustellen, wird die Narbenseite nur fein geschliffen. Hier wird behutsam per Polierschliff die eigentliche Struktur hervorgehoben. Ein typischer Glattschliff
findet häufig bei Krokodilleder statt.
Die Rückseite, die Fleischseite von Leder, wird verwendet, um Wildleder herzustellen. Hier wird durch ein sauberes Schliffbild das typische Velourlederaussehen erreicht.
Das AWUKO Schleifmittelsortiment umfasst eine umfangreiche Auswahl an Schleifmitteln für jegliche Lederverarbeitung.
CUMI AWUKO Abrasives GmbH
Finden Sie heraus, welches Schleifmittel die richtige Wahl für Ihren Produktionsablauf ist.
AWUKO Schleifprodukte sind in verschiedenen Leistungsstufen erhältlich.
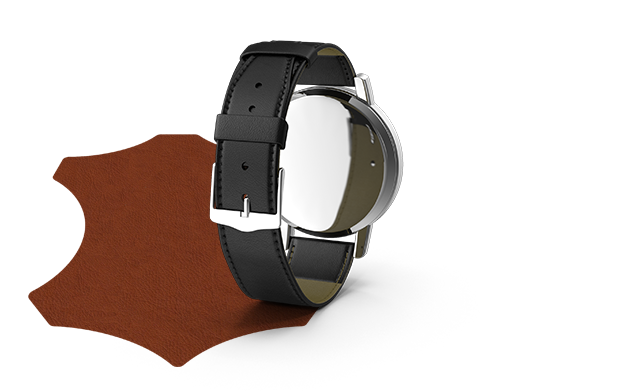
Welche Schleifmittelwahl ist die Richtige für Ihre Prozesse? Sie haben die Wahl; die gewünschten Ergebnisse mit den Kosten in Einklang zu bringen, die Sie bereit sind zu zahlen. Wenn der anfängliche Preis Ihre Hauptüberlegung ist, wählen Sie das AWUKO KP43E. Beachten Sie jedoch, dass ein niedrigerer Schleifmittelpreis im Voraus hinsichtlich der Standzeit möglicherweise nicht wirtschaftlich ist. Wenn Sie Anwendungen mit hoher Produktivität ausführen und die anfänglichen Schleifmittelpreise berücksichtigen müssen, ist es Zeit Schleifmittel mit längeren Standzeiten zu nutzen.
Lederbehandlung wie - Spalten - Schleifen - Trockenfalten
Das Entfleischen und Spalten der Tierhaut geschieht rein mechanisch. Nach der Bearbeitung ist die vollständige Aufnahme der später zugemengten Gerbmaterialien erst möglich. Diese Kombination aus chemischen und mechanischen Vorgängen sorgt für die organische Stabilisierung des Leders. Wenn die Lederteile aus dem mechanischen Einweichen (in den Gerbtrommeln) kommen, sind sie weich und spannungsfrei. Erst jetzt sind die Oberflächen bereit weiterverabeitet zu werden und sie nach den Vorstellungen der Veredler zu nutzen. Die Leder können jetzt sowohl von der Narben- als auch von der Fleischseite veredelt werden. Da eine einheitliche Gestaltung nur von der Narbenseite her möglich ist, muss vorab die Ledernutzung beschlossen werden.
Schleifen:
Das Schleifen des Leders verleiht dem Leder einen ganz besonderen Charakter, wie es von Wildleder her bekannt ist. Die Fasern auf der Oberfläche werden mit den scharfen Kanten der Schleifkörner auf eine gleichmäßige Länge geschnitten. Je feiner die Maserung, desto kürzer der Schnitt. Die Wildleder-Ledertypen Velour und Spaltvelour werden in mehreren Durchgängen mit immer feinerer Körnung fleischseitig geschliffen. Bei Nubuk ist der Kornstrich sehr fein und schleift das Leder sehr samtig. Hierzu wird das Leder mittels mechanischem Druck gegen die sehr schnell rotierenden Schleifwalzen gedrückt, während eine Oszillationsbewegung für den gleichmäßigen Schliff der gesamten Lederoberfläche sorgt.
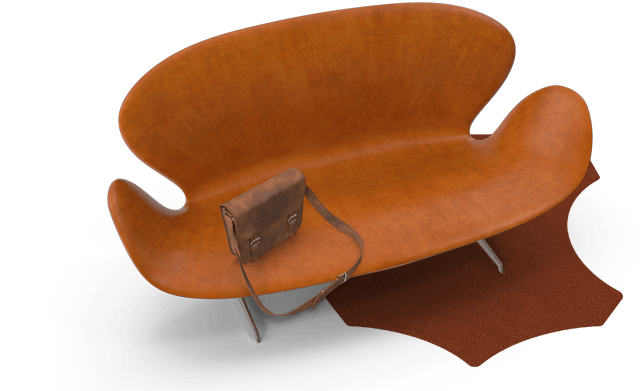
Auch bei einigen Arten von Narbenledern wird vor der Zurichtung die Narbenseite ganz leicht geschliffen. Dies soll z. B. nach einer Pasting-Trocknung die Kleber-Reste entfernen oder eine bessere Verankerung der Zurichtung ermöglichen.
Bei den pflanzlich gegerbten Ledern können sich die beim Schleifen entstehenden Temperaturen der Lederoberfläche nachteilig auswirken. Hier wird man eine Spanabnahme durch einen Schneidevorgang vorziehen. Das Trockenfalzen wäre ein solcher Arbeitsgang. Speziell für pflanzlich gegerbte Flächenleder kennt man das Blanchieren. Dieser dem Falzen vergleichbare Vorgang erlaubt nur geringe Spantiefen, denn die spiralförmig angeordneten Messer sind nur in einer Richtung angeordnet. Die blanchierte Lederoberfläche zeigt keine Bearbeitungsspuren. Die gefalzte Oberfläche zeigt einen ausgeprägten Streifen in Bearbeitungsrichtung.